What are the 7 QC tools? How to use it to improve quality control
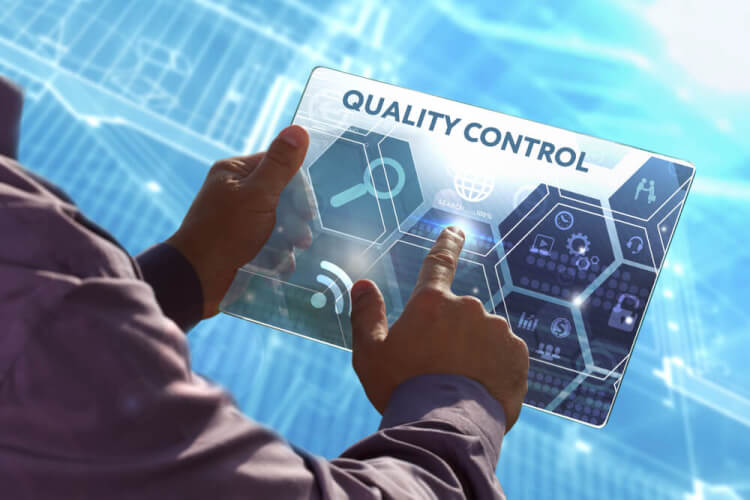
table of contents
- What are the 7 QC tools?
- graph
- Pareto chart
- Cause and effect diagram
- Scatter plot
- control chart
- Check sheet
- histogram
- Points to remember when using the seven QC tools
- “New 7 QC tools” used for quality control, improvement, new product development, etc.
- summary
What are the 7 QC tools?
The 7 QC tools is a general term for the methods used in statistical quality control, and the name “7 QC tools” comes from the use of 7 tools that are particularly effective for quality control. I am. Because it can analyze quantitative data, it has become popular mainly as a quality control and improvement method at manufacturing sites. By the way, the term “seven tools” refers to the seven tools of Musashibo Benkei, a famous vassal of Minamoto no Yoshitsune.
graph
Graphs are diagrams that can visually represent multiple pieces of data, such as line graphs, bar graphs, and pie charts. It allows you to express numerical values and ratios in an easy-to-understand manner, and is used when you want to visually check the overall situation. Basically we are dealing with two variables.
For example, when you want to compare the number of defective items by month, it is better to use a bar graph rather than a table to see at a glance which month the most defective items occurred. Using graphs when explaining things to others is easy to understand and effective. Histograms, scatter charts, and Pareto charts, which are listed as seven QC tools, are also graphs.
Pareto chart
A Pareto chart is a diagram that divides phenomena into processes and items and represents them using a bar graph and a line graph of occupancy. Originally, there was an idea called the Pareto principle (also known as the 2:8 rule), which states that 20% of the factors influence 80% of the total, and a Pareto chart can visualize this. Use this when you want to understand which process/item should be improved to have an effect.
For example, if there are 5 defective items for a certain product, create a bar graph showing the number of products in which each defective item was found in descending order. If you further overlay the cumulative ratios as a line graph, it becomes clear that most defective products are due to specific defects (for example, item 1 and item 2). Since you can find problems in order of importance, it becomes easier to prioritize which items should be addressed first.
Cause and effect diagram
A cause-and-effect diagram is a diagram that uses arrows to organize the characteristics of a problem and the factors that influence them. Use this when you want to understand the factors that are affecting a problem. A fishbone diagram is also called a fishbone diagram because the collection of arrows looks like a fishbone.
For example, in response to the question “Why did a defect occur in product A?”, list the likely causes of the problem, such as “procedure error,” “dark lighting,” and “no inspection process,” and connect them with arrows. . This will reveal what factors are related to the problem. Once we have visualized the relationship between characteristics and factors, we can proceed with discussions on improvement measures such as “creating a procedure manual that uses videos,” “increasing the lighting,” and “introducing an inspection process.”
Scatter plot
A scatter plot is a diagram that represents data as a set of points. Used when you want to check the relationship between two pieces of data. For example, if you want to investigate the relationship between the humidity in a factory and the number of defective products, the daily humidity in the factory and the number of defective products are aggregated as data, and the horizontal axis is the humidity (factor), and the vertical axis is the number of defective products. Take (results) and make a scatter plot.
By calculating the correlation coefficient (r) from these data, you can determine the degree of relationship. r takes a value from 1 to -1, and when there is a high relationship, it is said to be “positive correlation (negative correlation)”. By using a scatter plot, you can see at a glance whether two pieces of data are related.
control chart
A control chart is a line graph used to understand the state of a process from time-series data, and is used when you want to understand variations. In the graph you create, use the center line (average value/CL) as a reference, and write plus 3σ of the standard deviation as the upper control limit (UCL) and minus 3σ as the lower control limit (LCL). It is statistically known that in a normal distribution, 99.7% of the results are within 3σ of the standard deviation, and if the values do not exceed the upper and lower control limits, even if the values deviate significantly, they are considered to be a coincidence. Then, only when the value exceeds the control limit is considered an abnormal value, and the cause is investigated.
For example, you can obtain the number of defective products on a daily basis and create a time-series line graph. Then, draw the center line and the upper and lower control limit (LCL) lines. By creating a time series graph, you can easily discover numbers that deviate from a certain range (abnormal values). We will investigate the cause of what happened on the day the number of defects exceeded the control limit.
Check sheet
A check sheet is a chart-like sheet that allows you to record and inspect each classified item. Basically, it is the same as a check sheet that is used on a daily basis, and it is used to prevent omissions and keep records by marking whether or not items have been inspected according to the purpose. By listing items, anyone can inspect and record them in the same way.
histogram
A histogram is a column-shaped diagram in which data is equally divided into several intervals and the number of data that falls in each interval is plotted on the vertical axis, and is also called a frequency distribution diagram. Used to understand the distribution of the entire data. It is often used in statistics such as population distribution because it allows you to visually understand the distribution structure of the entire data. In quality control, we estimate what is happening by understanding the characteristics of variation using a histogram.
For example, if the histogram has a peak in only one off-center position (isolated island type), it is likely that the product in which the abnormality has occurred is included in that range.
Points to remember when using the seven QC tools
When using the seven QC tools, the key is to be aware of “which method can solve the problem” and “what kind of data is needed when applying the tool.”
If a problem occurs in quality control, you can understand the situation and the cause of the problem by applying the data to one of the seven QC tools, similar to frameworks such as SWOT analysis. By understanding the characteristics of each tool, it will be easier to make decisions such as “I think a Pareto chart can be used in this situation.”
Also, when considering what kind of data is needed, the concept of “stratification” is useful. This is a method of organizing data based on a certain perspective, such as by time or worker, and allows you to grasp the characteristics and trends of the data. It is positioned like a pre-processing process that uses seven QC tools. Apply stratified and organized data to one or more of the seven appropriate tools. You don’t have to use all the tools.
“New 7 QC tools” used for quality control, improvement, new product development, etc.
The new seven QC (Quality Control) tools are quality control methods developed primarily for administrative staff. While the conventional 7 QC tools were a method for managing numerical data, the new 7 QC tools are a method to clarify problems by organizing linguistic data that cannot be quantified into diagrams.
The seven new QC tools include “affinity diagramming,” which organizes linguistic data by grouping it, “association diagramming,” which connects causal relationships between causes and effects with arrows, and “systematic diagramming,” which systematically shows objectives and means. “Matrix projection method” which arranges two-dimensional elements in two dimensions, “Matrix data analysis method” which analyzes the data of matrix projection, “Arrow diagram method” which clarifies the process and schedule for solving a problem, “Arrow diagram method” which shows alternative plans. There is a PDPC method.
summary
The seven QC tools have long been used in many workplaces as a statistical quality control method. In particular, Pareto charts and characteristic factor diagrams are useful tools in today’s manufacturing sites. Study the characteristics of each of the seven QC tools on a daily basis and be prepared so that you can take prompt and appropriate action even if a defect occurs.